Quality Management
The entire team at Iron Networks, Inc is totally committed to quality. We always put the customer first in all that we do. Our quality management system is continuously monitored and improved to ensure that all our services and products offer the highest standards of quality and reliability. The Iron Networks Quality Management System is ISO 9001:2008 Certified.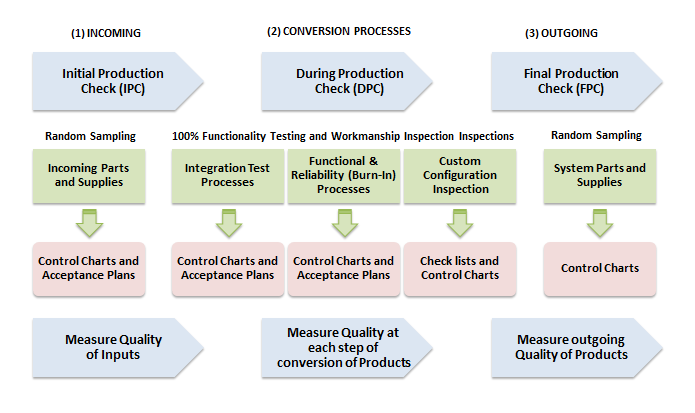
Quality Policy Statement:
- The scope of Iron Networks business activity encompasses procurement, manufacturing, engineering and distribution of network equipment and accessories, including software configuration.
- Iron Networks recognizes the need to focus its business on ensuring high quality performance throughout the organization.
- This commitment to quality is based on effective and consistent operational systems, which are continually monitored. The primary goal is the satisfaction of customer needs.
- Certificate Copy: It is the policy of the Company to meet this goal through the continual improvement of its activities. This improvement is achieved by establishing measurable quality objectives at all levels of the organization. Performance against these objectives and opportunities for improvement are regularly evaluated and responded to using the company’s Management Review process.
- Consistently high quality performance results from a management system that provides clear standards and guidelines in all the appropriate areas of the Company’s activities.
- It is the policy of the Company that its management system will continue to provide an effective tool to satisfy the requirements of its customers, the specifications of the ISO 9001:2008 Quality Management Systems Standard, and all legal and regulatory obligations.
Quality Assurance Capabilities:
- An advanced documentation control system (Agile) and operational portal system that will provide and ensure that only the most current documents are being used and are guiding each operational process in a highly dynamic manufacturing environment.
- Use of SPC, a three-stage quality controls process (in materials, work-in-process and finished products) ensures that the clients' quality requirements and/or specifications are fully met.
- Product and Quality Engineers who provide an engineering Failure Analysis (FA) based on the clients' specific requirements and/or coordinate a FA with designated suppliers, or a third party if needed.
- An advanced data recording system and real-time web-based quality reporting system that will provide the client with information about the product quality history at its specified requirements.
- An effective internal quality system that processes roving audits that integrate Corrective Actions (CA) and/or Preventive Actions (PA) that help to improve the daily manufacturing operations.
- EU RoHS and WEEE Directives compliant. This helps to provide assistance to clients and coordination with suppliers.
Quality Focus:
Realizing that quality is driven by the client we seek to acquire success and provide exceptional solutions and services in the following areas:
- Exceeding Clients' Needs and Expectations.
- Client Communication and Total Client Satisfaction.
- On-Time Delivery and Customer Support.
- High Quality Performance and Defect-Free Products.
- Cost-Effective Operations and Processes.
- Continuous Improvements to Processes both Internally and Externally.
Quality Management:
Our management's key focus is to meet clients' requirements and deliver a product that generates a high level of satisfaction. Management will continually seek to improve in these efforts by conducting a frequent measurement analysis, and evaluation of the management of our Quality Department's resources. Such resources include:
Quality System: QM Document Control.
Quality Training.
ISO Standards Compliance.
Document Support for QA and Quality Engineering.
Quality Assurance:
Quality Auditing
CAR/PAR
Client Quality
Supplier Quality
QA Reports
Quality Engineering:
SOPs and WIs
Product Quality Plans
Test/ Insp Spec./ Standards
Measurements
Metrology
FA & Reliability
Process Control SPC
Technical Instruction for QC and QA
Quality Control:
Incoming Material QC
In-Process QC
Finished Product/OOBA
QC Reports